Advanced Warehouse Management: Best Practices for Temperature Control & Intralogistics of Perishables. Part 2

Director of Operations
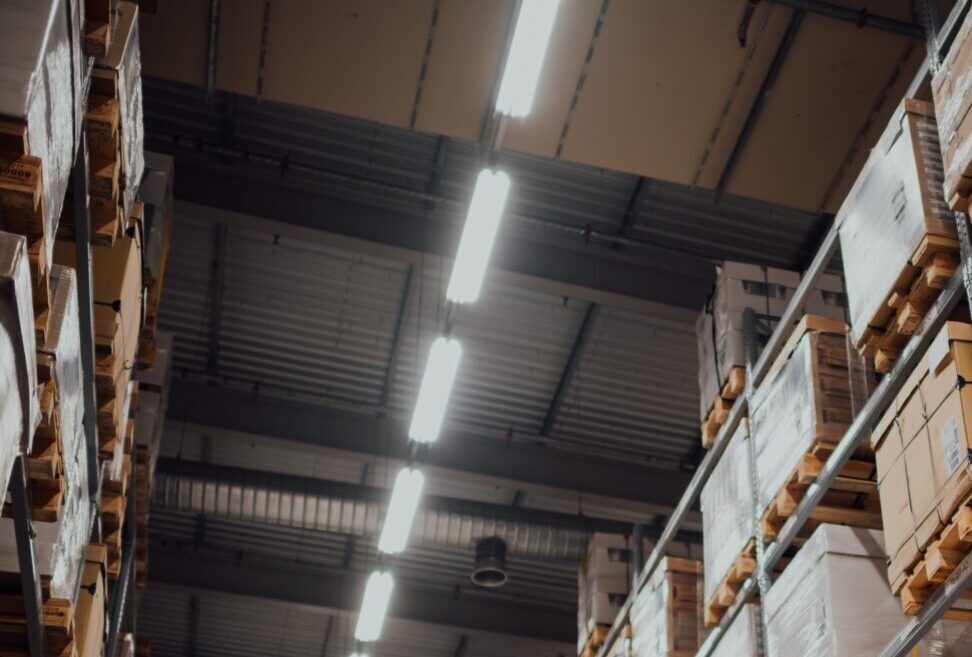
In Part 1 of our series, we explored the key components of effective cold storage warehousing, strategies for optimizing temperature control and movement, and the importance of monitoring product temperature.
As we continue our exploration of cold storage warehousing, it’s essential to grasp the broader context. Annually, the global food system witnesses the loss and waste of over 1.6 billion tons. This staggering amount equates to 13% of global food production, enough to sustain 950 million individuals.
The advanced challenges and solutions below play a crucial role in the storage of perishable goods and help mitigate these losses.
Warehouse Storage Optimization
Optimizing storage is crucial, especially in warehouses with multi-deep cold/frozen storage. The primary goal is to ensure storage cells are filled to capacity, preventing numerous cells from being only partially occupied. This avoids excessive energy consumption associated with cooling half-empty cells. If not carefully designed and managed, such warehouses can lead to significant energy wastage.
To achieve this level of efficiency and precision, several components and strategies come into play:
Ensuring Product Quality and Energy Efficiency
This careful planning is particularly critical during the storage and order picking of frozen products, especially in manually operated warehouses. The focus is not only on cost considerations but also on the preservation of product quality within the warehouse. As a software company, we aim to contribute to energy efficiency by implementing effective WMS processes that ensure the integrity of the cold chain.
Addressing Storage and Zoning Criteria
Utilizing address storage enables distinct storage regions within the warehouse, each requiring specific operational technologies. These regions, known as work areas, consist of a cluster of storage cells determined by the employed operational technology. This zoning criterion is based on the storage needs of the goods.
For instance, products demanding varying temperature and humidity conditions for storage, like fresh vegetables, dairy products, and frozen foods, should have separate areas. The Warehouse Management System (WMS) meticulously oversees the occupancy of cells within the refrigeration zone.
Leveraging Advanced Technologies for Space Efficiency
The use of complex automated or robotized systems integrated with a WMS can be deployed to ensure efficient use of space. These systems are designed to allocate space strategically, ensuring consistent filling of storage to maximum capacity.
It’s essential not only to relocate items efficiently but also to manage their wait times in the queue for an order. When assembling an order from components stored in various zones, all components should arrive at the picking and loading area simultaneously, minimizing idle time.
Other Unique Challenges of Managing Cold/Frozen Storage Facilities
Refrigerated warehousing introduces additional layers of complexity that go beyond typical Warehouse Management System (WMS) capabilities. These complexities often arise from the need to manage items that aren’t standard goods or SKUs.
Cold Accumulators: An Integrated Approach
Cold accumulators, used as supplementary cooling agents during product movement within the warehouse, aren’t classified as standard products. Yet, their role is vital and requires integration into the WMS.
When a transport container moves through the warehouse, the WMS directs the placement of these accumulators. As goods reach their storage area, accumulators are removed. The challenge lies in embedding this workflow into the WMS, something many solutions might not support.
At First Line Software, we’ve successfully navigated this challenge for our clients.
Goods with Restricted Access: Enhanced Tracking
Another complexity involves the processing of items with controlled access, such as poisons or potent drugs. These items demand not only distinct storage areas but also meticulous tracking during their warehouse transit. This precision ensures safety and adherence to regulations, highlighting another arena where advanced WMS solutions prove invaluable.
Achieving Peak Performance in Cold Storage
The intricacies of refrigerated warehousing go beyond just its design and layout. To ensure optimal operations, it’s essential to address other factors, such as:
- Complex Topology: The physical design of refrigerated warehouses often requires special considerations, especially in more intricate storage setups like multi-deep storage areas. Here, containers might have to be relocated temporarily for access, introducing operational challenges.
- Strict Requirements: Efficient operations demand:
- Effective put-away and picking processes, especially in multi-deep storage areas.
- An uninterrupted cold chain to ensure product quality.
- Reduced human involvement in cold zones for safety and efficiency.
- Simplified manual tasks given the protective gear that constrains human mobility.
- Automation and IT Demands: Elevated automation, while beneficial, introduces unique IT solutions and implementation requirements. Advanced Warehouse Management Systems (WMS) are central to navigating these complexities.
Luckily, our advanced WMS solutions, tailored for refrigerated warehousing challenges, can optimize these processes. If you seek a partner for these challenges, our experts are poised to assist.
Navigating the Cold Storage Landscape with First Line Software
The intricacies of cold storage require expertise and specialized solutions. First Line Software provides tailored warehouse management solutions to address these unique challenges. Partner with us for reliable assistance in refrigerated warehousing.
Contact First Line today to learn more about our warehouse automation services.