Digital Twin in Manufacturing: Frequently Asked Questions
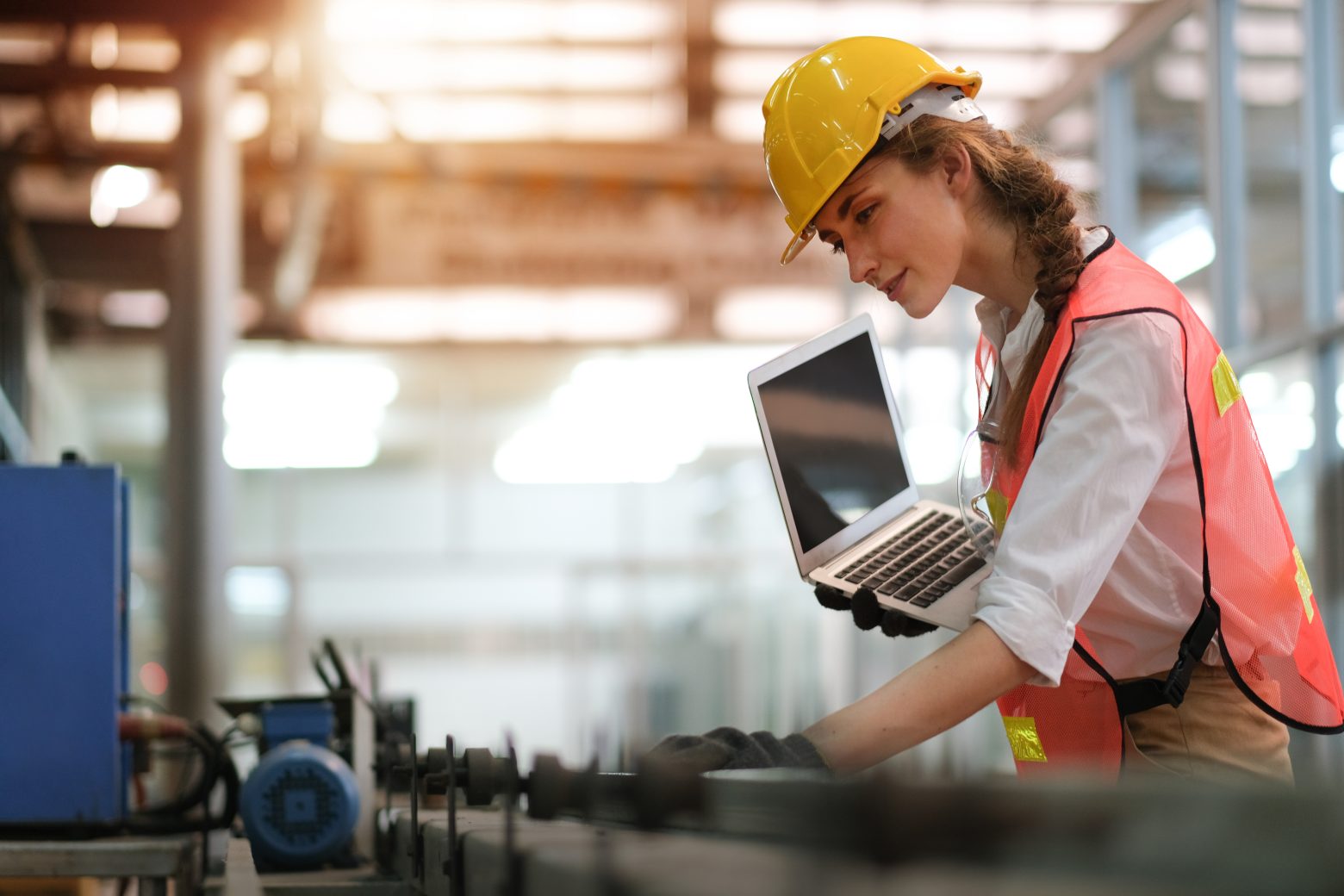
The Digital Twin market is expected to grow from USD 6.9 billion in 2022 to USD 73.5 billion by 2027; it is expected to grow at a CAGR of 60.6% from 2022 to 2027.
A Digital Twin is a virtual prototype of real production assets – wells, turbines, wind turbines, etc. This is a complex software product, it is based on a wide variety of data and numerous IoT sensors. The digital model helps to change the parameters of the equipment and makes improvements much faster and safer than experiments on real objects.
The Digital Twin allows production to significantly expand the capabilities of cloud analytical services used in the concept of the Industrial Internet of Things (IIoT) in the fourth industrial revolution.
Let’s take a look at why this technology is so important for the manufacturing environment.
Data-Driven Operations
Enterprises need to evolve their production systems to support so-called data-driven adaptive operations, where systems automatically respond to known and new scenarios. However, this is easier said than done. As manufacturers seek to move towards adaptive operations, they are hindered by the traditional and isolated architecture of manufacturing systems. These older systems limit cases beyond individual assets and single functions, thereby preventing massive amounts of data from being collected, integrated, and analyzed.
That is why the concept of Digital Twin is attracting more and more attention from business leaders. The Digital Twin is based on the ability to combine data from various sources and unify and contextualize them. It offers a single solution for people and applications that can use the contextualized data repository for a variety of purposes.
Manufacturing executives are exploring the possibilities of Digital Twin, but uncertainties remain about their implementation. Below are the most frequently asked questions and their answers.
Why is Digital Twin Changing the Market Rules of the Game?
Digital Twin not only processes data but also presents it in the appropriate context. They allow manufacturers to capture information and display relationships throughout the organization, guiding it in the direction of evolution toward fully autonomous operations. Traditional architectures of isolated production systems face problems related to heterogeneous information. Combined with the lack of a contextual data environment, engineers working with these systems struggle to extract valuable insights that enable them to optimize business operations.
Digital Twin technology enables progressive learning and knowledge, which is key to achieving autonomous operation. In fact, this technology stores and structures information that engineers and operators can understand. It ultimately reduces the dependence on data analysts to solve day-to-day issues, and leads to an increase in the efficiency of the organization.
Digital Twin gives engineers and operators control and accountability for production data and related decisions. By combining the power of the digital twin and modern low-code/no-code tools, manufacturing leaders can provide data engineers with a safe space and they can collaborate to develop new ways to optimize operations.
Is it Possible To Use Digital Twin Without Replacing All The Underlying Solutions?
The answer is yes. A comprehensive and unified manufacturing architecture remains the backbone of manufacturing operations across all industries. Industrial leaders can implement Digital Twin in parallel with existing systems. Using this “twin” data, the Digital Twin allows manufacturers to extract more value from years of investment without the need to “uproot and replace.”
Using the power and flexibility of cloud platforms and technologies, the Digital Twin allows manufacturers to capture data from IT and OT systems – from ERP to programmable logic controllers, supply chains, and distribution – and quickly and efficiently contextualize it.
Although it does not require a complete overhaul of traditional systems to take advantage of this technology, it may partially affect previously integrated systems. Manufacturing leaders should work to streamline their existing manufacturing architecture to:
- Create a data-driven template approach and an abstraction layer that allows you to simplify and standardize the system without the need to replace expensive equipment on-site.
- Transfer valuable specific developments (for example, a violation of conditions in the upstream that can cause failures in the downstream), most of which are related to data and artificial intelligence, to the environment of the twin.
- Strengthen the “vertical” integration of ERP and shop floor systems, which creates a reliable and efficient execution mechanism.
- Integrate execution and optimization with digital twin over time.
How Do MES vendors position themselves in relation to major cloud platforms and IoT vendors?
Manufacturing Execution Systems (MES) are the backbone of the modern IT/OT stack. They will continue to play an important role as more manufacturers move towards next-generation manufacturing operations management (MOM) architectures. MES vendors are evolving their solutions to increase their reach while leveraging the flexibility of the cloud, facilitating their integration into next-generation manufacturing architectures. This is due to increased competition from IT players, including both specialized startups and cloud providers.
Suppliers continue to expand their offerings and portfolios, focusing on platforms including data historians, quality management systems, asset performance management systems, and warehouse management solutions. Today’s market leaders offer a much broader range of core capabilities complemented by industry best practices, which enables faster deployment of systems with limited customizations.
Another major trend in the industry is the deployment of cloud solutions. It greatly facilitates integration into the overall MOM architecture and reduces the cost of deploying MES, while making it easier to implement the system at different sites. In addition, MES providers are increasingly providing more flexible offerings that can help manufacturers with limited budgets and limited capacity move from large capital investments to a subscription model. Combined with accelerated deployment, this makes MES implementation more cost-effective. These changes have brought MES to the attention of decision-makers in the development of Industry 4.0 roadmaps.
What Did We Learn?
The data shows digital twin technology is growing fast – around the world and in manufacturing and enterprises. Manufacturing units across the globe are investing in digitalization strategies to increase their operational efficiency, productivity, and accuracy. Early adopters will have a head start on bringing better products to market faster than their competition. As your primary IT software partner, First Line Software will partner with you in your drive to create Digital Twin. Talk to us today!