Risky Business in WMS
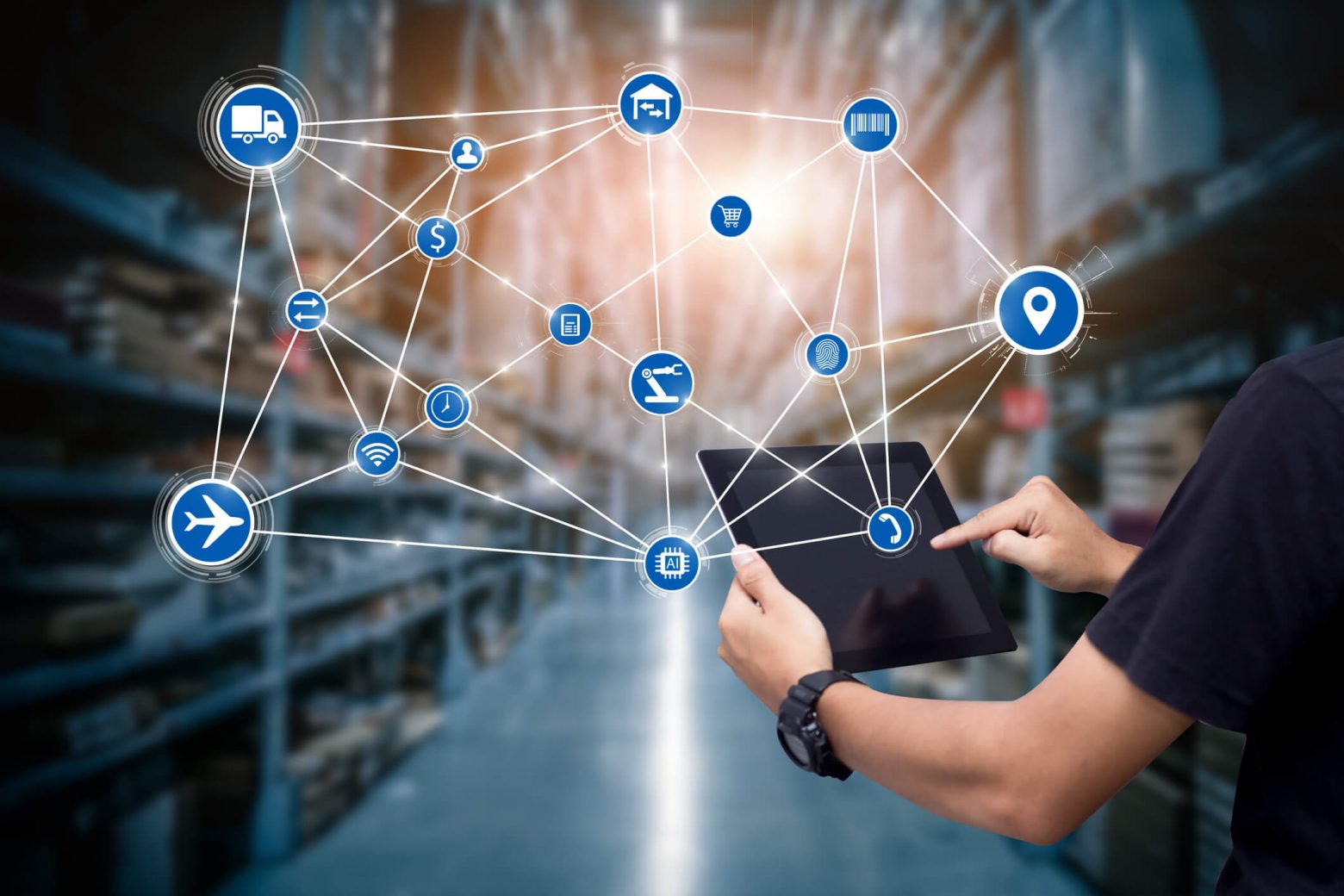
The title of the classic 80’s movie may have caught your attention, and although Tom Cruise’s character in the movie certainly didn’t require a Warehouse Management System, if you’re reading this you might be considering implementing a WMS solution in your own business. This article will highlight six major aspects that can expose you to risky business decisions leading to a compromised WMS launch. It’s not meant to cover every scenario, but the six-point check list is a starting point which you apply to your own unique environment to help mitigate risks in your WMS journey.
However, before we get down to (risky) business let’s take a quick look at where the global warehouse automation market is trending as of late. LogisticsIQ’s latest post-pandemic market research study is based on an analysis of 650+ companies with more than 100 in-depth interviews. They concluded that the Global Warehousing Automation Market will reach the milestone of $30 billion by 2026, at a CAGR (Compound Annual Growth Rate) of 14% between 2020 and 2026. These figures are important to note as the pandemic has accelerated e-commerce sales and more companies wishing to stay competitive are ramping-up their WMS programs. Faster fulfillment, a shortage of labor, and higher wages for warehouse personnel all add up to even small to medium-sized businesses looking to adopt WMS solutions.
Once you start looking at a warehouse management system as not just a “want”, but an important part of a “need” to stay competitive, you’ll want to read ahead to see what pitfalls to avoid as you start your journey. Here are six major aspects within the scope of implementing a warehouse management system to look out for when mitigating risks in your own situation:
- Technical – Choice of supplier & system
- Business – Changes in processes
- Human – Adoption of changes
- Planning – Miscalculating deadlines
- Deployment – Remote startup pitfalls
- Change – Financing, strategy, and people
The technical
This first aspect will undoubtedly be the most important decision you’ll need to make when beginning your WMS project as it will affect the other five to one degree or another. Choosing the right supplier or vendor will give you the best chance for implementing the optimal system for your application. The preferred play here is to utilize the “one-vendor” concept where the ideal vendor is one that can supply both the software and hardware (conveyors, robots, cranes, etc.) Now “supply” does not necessarily mean all the products are proprietary to the vendor, but that the vendor is providing a comprehensive, complete eco-system. This route ensures smooth automation integration, easier future updating, and consistent servicing of both software and hardware installations. Not every WMS developer vendor can claim experience in these significantly complex processes. However, this “one-vendor” route might not always be possible and may not be the optimal route for your given situation, especially if the products of different vendors suit you the best. In either case, take your time in searching for a vendor with a similar attitude towards business and corporate culture as your own.
Now the choice of the actual system itself will likely be done in conjunction with your selected implementation vendor, but an important question to ask is whether to initiate the conversion with hardware or software. We’ve covered this topic in greater detail here, (LINK TO ARTICLE) and not surprisingly your company’s own business process will determine which comes first. Most organizations looking to implement a WMS solution will likely have some existing hardware and equipment in place and wish to integrate this infrastructure with software to run it more efficiently. However, speaking to your vendor about the many different options available to you based on your needs should be a conversation initiated by you, the client. The compatibility of disparate existing hardware and/or software can be overcome with an experienced vendor skillfully employing today’s modern technology.
The business side
Even though it’s in our nature to minimize change, let’s look at how embracing change when it comes to automating your warehouse can pay off in ways you may not have considered before. It starts with the ever-difficult task of looking within your company to define your business processes. This comprehensive front-end business introspection combined with a careful WMS vendor selection will help determine the optimal configuration of your space, and the necessary equipment options to make it work. After defining your processes in detail, you’ll be faced with two questions:
- Do you fully automate your warehouse based on the existing processes
OR
- Do you implement current automation industry standardized processes?
Let’s “cut to the chase” here and state that the preferred approach will be to implement current automation industry standardized processes whenever possible. In many European countries and elsewhere in the world, there are certain benchmarks or standardized criteria to be met when implementing a WMS. However, this may not always be feasible and in reality, it’s often necessary to find optimal compromise solutions when existing warehouse automation is partial, or a simplified accounting process for goods is being implemented. Compromises such as these are due to the fact that sometimes when you’re simulating an automation scenario in your warehouse (which you should always do) it may reveal the emergence of complex, ineffective processes, without which the final system significantly benefits.
The human aspect
Statistically speaking, your warehouse is likely to be mostly manually operated (research shows that 80% of current warehouses are still manually operated with little to no supporting automation. Just 5% of existing warehouses are fully automated-meaning completely roboticized). Therefore, people still are the primary movers of goods and materials throughout most facilities, perhaps with some equipment and systems to help the process along. This “process” as mentioned above is a key part of your business analysis.
For some clients, the underlying premise might be that in their manual warehouse, the daily execution and regulation of the process is their strength. Other clients may come to the conclusion that their existing process is a weak point and needs redoing. People can work relatively efficiently under somewhat structured guidelines, but in a manual warehouse processes are more-often-than-not invented on the fly with circumstances dictating the immediate need of an action. This is essentially a creative attempt to control chaos in the warehouse by finding optimal solutions to various problems at specific points in time.
It may seem obvious, but involving the major and minor personnel in your existing warehouse operations early on in conversations about adopting a WMS will better your chances for a smooth implementation. Let your employees know that automation and digitalization is a natural evolution of their working environment, and is meant to help them do their jobs more efficiently rather than reducing their numbers. Simply put, the WMS will help them focus on more valuable tasks thereby growing their skills and their careers. Putting together a team of individuals that represent all of the stakeholders in your warehouse operation that have a hand in the process is a great way to help mitigate the inevitable concerns about change and what that means to your people.
The planning
Ask anyone who has rebuilt a classic car, remodeled a kitchen, or organized a wedding… things rarely go as planned. However, a classically reasoned analysis of the requirements needed to implement a WMS might be approached just like someone were to plan an automobile restoration or a complete home remodel, however this is not the correct approach. An objective analysis of the needs of the company (see The Business Side above) will drive the successful planning of the WMS and help achieve realistic implementation goals.
One study shows that on average, companies spend approximately fifteen weeks just in the selecting of a vendor/system and subsequent planning of a WMS system; all before any actual facility deconstruction or construction were to begin. The “go-live” date to start using the system must be derived from a specific list of tasks linked to the workers responsible for them, as opposed to a wishful date or time. The goal is to have a comprehensive punch-list of steps needed to get to your “go-live” date, with each job’s completion time realistic to the complexity of each step, and the scheduling of the individual or team responsible for the activity.
The remote deployment
In a typical WMS implementation prior to our global healthcare crisis, an in-person warehouse visit by the installing vendor was necessary to understand how the facility was operating. The vendor came to observe and speak to people in various operational roles such as pickers, forklift operators, maintenance staff, etc. As on-site visits can be challenging today, another approach to compensate for the lack of face-to-face meetings uses a technology we all have in our pockets. Basically, a representative of the client virtually walks around the warehouse simply using his or her smartphone camera.
However, when it comes to the technology and the need for implementing a WMS; forward-thinking companies have realized the efficiency and competitiveness of implementing and maintaining a warehouse remotely before our global healthcare crisis began. So this is not a brand-new way of doing things borne out of our current situation; but today it’s most certainly accelerated by it.
Even though there are many advantages to remote implementation, there still can be challenges to keep in mind depending on the complexity and size of the situation. If the contracted vendor lacks an opportunity to visit the warehouse directly to see the business processes with their own eyes, they might miss the opportunity to personally talk to the employees who will be involved in the solution development process. In addition, for complex cases that require extensive discussions, gaining an understanding of processes, and joint decision-making – the remote format may take a little more time. However, none of these issues are insurmountable and shouldn’t deter anyone from seriously considering remote implementation.
The idea of change
Fungibility in our daily lives is something we’ve all come to expect in recent times. As humans we’re generally resistant to it so it’s usually uncomfortable for most of us to initially embrace it. A business’s job is to grow, and the people and technologies running that business are the ones responsible for that growth. A few of the main things that drive a businesses’ growth, (yet are most susceptible to change – therefore risk) are likely to be financing, strategy, and most importantly people.
In some cases, the financing allocated to a WMS project is exhausted prior to completion. The primary cause of this goes back to our planning process. The difficulty of tasks was underestimated and human resource availability ended up being lower than calculated. Various issues that impact budget and schedules are expected in any implementation. One way to hedge against failure by a financial shortfall is to consider a “contingency reserve” fund into your budget.
Luck plays a major part in success, but having a sound strategy makes it easier to capitalize on lucky opportunities. When you decide to implement a WMS can be just as important as how you’ve gone about doing it. One strategy is to implement your system after a known busy period, keeping on some of the best of the temporary peak season workers so that the WMS can be successfully implemented during a slower time with a minimal impact on operations. This strategy can also minimize the risks of any unexpected delays in the implementation.
It’s been said before, but it bears repeating that people are the greatest resource in any business. Technology does not care whether change happens or not, but people working in a warehouse are acutely aware of any shift in the rhythm of the machine that is their environment. The primary way of avoiding risk in this sensitive area is through training. With the complexity of new equipment, there needs to be adequate staff education in the testing phase before the go-live date. There is no simple risk avoidance tip here other than to prioritize cross-training for everyone employed in the facility. The investment will be paid back many times as opposed to implementing a system where people aren’t confident in their WMS abilities and subsequently, your trust in them.
Regardless of what we do to mitigate it, business will always be risky. Hopefully, this article can help you avoid a pitfall or two that may not have been already anticipated in your initial research in implementing a Warehouse Management System.