Time to take stock?

Recent supply chain disruption and unpredictable demand mean that inventory optimisation has arguably never been more important. Head of Warehouse Automation for AMHSA member, First Line Software, takes a look at the benefits of keeping the right amount of stock.
Holding the right amount of stock is a delicate balance. Too little and you risk lost sales and upsetting customers by being unable to fulfil their orders. Too much and you tie up capital and risk all kinds of additional costs that put you at a disadvantage compared to your competitors.
Hence inventory optimisation – having the right amount of inventory available to meet present and future demand – is key for any business. In fact, inventory optimisation is so crucial to business success today that many leading companies are leveraging it to achieve and maintain competitive advantage. With today’s high consumer expectations and significant supply chain disruption – resulting from the ongoing pandemic and instability in some regions of the world – optimising inventory has possibly never been more important.
A complex task
Depending on the type of business, inventory can include not only finished products but also raw materials or components, work-in-progress, packaging materials and other supplies required for maintenance or operations. Hence inventory optimisation can be a complex task but, like many things in life, there is software to take care of it. Of course, most companies choosing to automate their logistics operations will benefit from a Warehouse Management System (WMS) and Inventory Management module to optimise their inventory for them. A WMS is responsible for inventory management inside the warehouse (optimisation of load placement in the racking, internal replenishment of bigger units to smaller ones, implementing the chosen inventory strategy and so on). An Inventory Management module is responsible for analysing stock levels in the warehouse and generating orders for external suppliers to replenish the stock. Inventory management must be integrated with the WMS and ERP (Enterprise Resource Planning) system and can either be a module of the WMS or ERP or a stand-alone system.
The benefits
So, what are the benefits of optimised inventory? As already mentioned, product availability is a key one. If products are in stock, you will avoid lost sales and margin dilution, the cost of processing refunds and customer dissatisfaction. Better stock visibility will allow you to improve lead times, enhance the customer experience and avoid firefighting, as well as the need to expedite orders.
Then there is the cost of capital being tied up in inventory. This restricts freedom in financial decision making and limits the opportunity to use this capital for other means, such as investing in more production capacity.
The risk of obsolescence is another factor. The longer you have unsold stock, the greater the chance that it will become outdated and need to be heavily discounted or even written off. Equally, holding inventory for long periods increases the risk of spoilage through, for example, flood damage, fire or theft.
Optimising inventory means minimising your inventory costs. It might sound obvious, but the more stock you have, the more handling is involved. For manual warehouses, that means more labour and for automated facilities it means more energy costs. Whether your site is manual or automated, storage costs money. Even if you own your building, stockholding means that space cannot be used for other purposes. In addition, you will probably pay higher insurance premiums if you keep a higher inventory.
Real-time visibility
Investing in a WMS that works in tight cooperation with the Inventory Management module and ERP can make it much simpler to optimise your stock at each point in your business cycle. With a WMS, you gain real-time visibility of your inventory, which allows you to work more collaboratively with your supply chain partners. By incorporating an ERP module, you can tap into data from suppliers to monitor their inventory levels, track shipments and order new stock automatically.
Holding the right amount of stock is a delicate balance. Too little and you risk lost sales and upsetting customers by being unable to fulfil their orders. Too much and you tie up capital and risk all kinds of additional costs that put you at a disadvantage compared to your competitors.
Hence inventory optimisation – having the right amount of inventory available to meet present and future demand – is key for any business. In fact, inventory optimisation is so crucial to business success today that many leading companies are leveraging it to achieve and maintain competitive advantage. With today’s high consumer expectations and significant supply chain disruption – resulting from the ongoing pandemic and instability in some regions of the world – optimising inventory has possibly never been more important.
Demand forecasting
There are numerous techniques that help to optimise inventory. Modelling and simulation can be used as part of the supply chain design process, with opportunities being identified for reductions in safety stock in various parts of the system. Supply chain planners can also use scenario analysis to ascertain inventory and service level outcomes in various what-if scenarios. Demand forecasting is used to predict required inventory for various products depending on factors such as market trends, product lifecycle stage, seasonal demand and promotional activity. Statistical formulae can be used to calculate safety stock levels and reorder points to ensure supply continuity.
Inventory strategies
Various inventory strategies can be deployed within a WMS, depending on the nature of the business. These range upwards from the Just-In-Time (JIT) strategy, which requires no inventory at all. A popular strategy is ABC analysis, which classifies inventory into 3 groups (A, B and C) based on product importance in order to prioritise goods that sell faster and are more profitable and optimise the storage of goods in the warehouse.
AI and analytics
Although an inventory management system can seem an expensive investment in terms of both the software and the required training, its benefits are undeniable. With all items scanned on entry to the system and removed on dispatch, accuracy is increased. In an automated handling system, the fact that this scanning is done automatically increases productivity by eliminating the time taken to manually track inventory. The knowledge of precisely what stock you have (via the WMS) and when more will arrive (via the Inventory Management system) helps to prevent overselling, which leads to customer disappointment. In addition, software – much of which is now powered by AI – brings insight and analytics that can help with demand forecasting and procurement planning. The digitalisation of inventory has enabled the concept of the ‘digital twin’, which compares the real world against what was planned. This approach brings valuable insight in terms of the stock that is required and how inventory needs are affected by factors such as demand volatility and supply variability.
Selecting a WMS
What should you think about when selecting a WMS and inventory management software? Of course, the WMS needs to help you monitor and manage your stock easily. As well as real-time information, it should offer at-a-glance data dashboards and advanced reporting features. Flexible and customisable workflow automations are also very useful features, along with the ability to integrate with other software that you already use such as marketing, payment and project management tools.
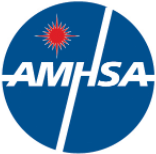