Strategies and Tactics to Maintain Competitive Edge in Warehousing Industry 2023: Part 1
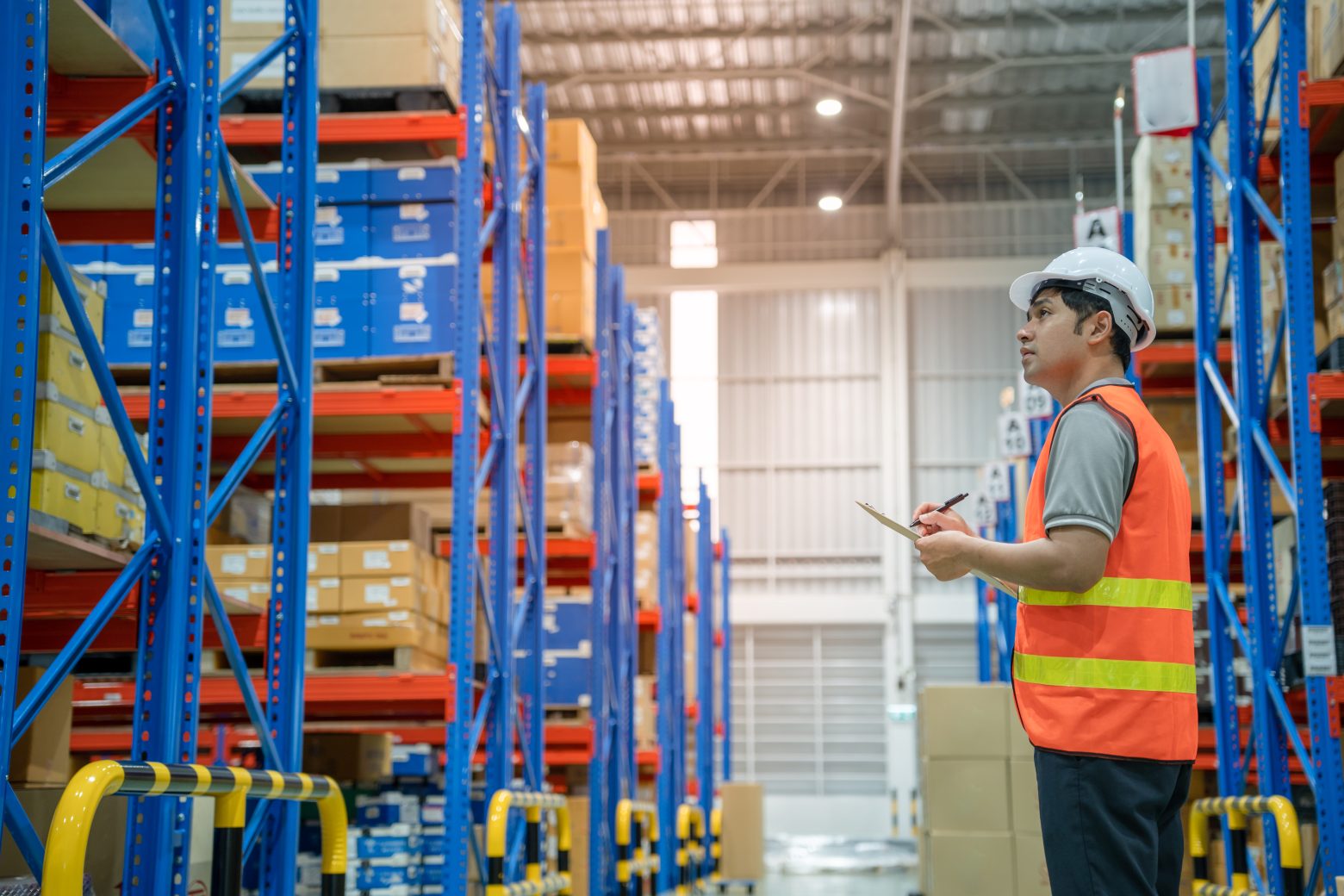
Considering our logistics and warehousing industries are all about technological progress, it seems like we’re living through a period of particular upheaval. Industry 4.0 is a much-touted idea that is becoming more completely realized as technology catches up with ambition. The question is: what defines a modern warehouse system? On the one hand, there are smart operations that allow the warehouse to work efficiently and automatically. On the other hand, businesses need efficient maintenance of these complex systems, and software support is also turning into a highly specialized, smart process.
Although automation has traditionally been used to handle repetitive operations and simplify rote ones, today’s automation systems are far more sophisticated and not only automate simple tasks but also workflows, and decisions, and even enable the autonomous supply chain. The main trends in warehouses are being directly influenced by this modern technology. For example, companies use a variety of maintenance strategies to boost efficiency and cut expenses. An asset must undergo a set of procedures we call maintenance to uphold its functionality and efficiency. Maintenance can be performed in response to a failure or as actions that were preplanned.
A non-optimized maintenance approach can lower an industrial plant’s output capacity by 5 to 20%, per Deloitte research. Additionally, recent studies have shown that industrial enterprises lose 45 billion euros annually due to downtime.
Smart Storage
Warehouse Management Solutions (WMS) are already used by the majority of warehouse operations, but under Industry 4.0, they would be “souped up” WMS combines enterprise resource planning (ERP), material flow control (MFC), and a programmable logic controller (PLC) that would serve as the brain of a sizable digital operation, gathering data and transmitting commands to a horde of mobile, autonomous, and semi-autonomous systems.
ERP systems oversee daily operations including accounting, finance, procurement, project management, supply chain management, and manufacturing. Enterprise resource planning (ERP) systems make it simple to determine how long an operation might take to complete, but a standard measurement needs to be determined through the use of a sample method or time study.
The control and coordination of the material flow in warehouses and distribution centers are made possible by the material flow controller (MFC). The MFC allows for flexible control of components from several producers ensuring independence from the producer’s software. The warehouse management system or another software/host system sends the MFC transport orders, which it then executes to direct the transport units to their destination.
The last stage is the programmable logic controller (PLC). PLCs in logistics operate as follows: the processor interacts with higher-level software, which interprets data from the warehouse management system and performs duties in accordance with preprogrammed regulations. These sorts of microprocessors, which are typically more durable, work in real-time, executing machine actions via output channels after receiving information via input channels.
Only one or two human operatives would be responsible for monitoring the whole WMS system, which would be used to catalog and manage every task.
These complete WMS systems offer many advantages for businesses. Robots can do tasks faster than people since they are aware of their exact location. In addition to reducing waste and the possibility of overstocking or understocking, more precise inventory control would also improve health and safety. Additionally, environmentally friendly procedures would be optimized, such as the usage of rechargeable batteries and robotic excursions to charging stations. The usage of augmented reality tools, such as heads-up displays on glasses, can also improve the performance of human workers by enabling them to discover and choose products or take in instructions faster than with conventional tools. The sum of all these advantages would increase the effectiveness of warehouse and logistics operations, which would be a significant step toward reducing delivery times.
Adapting to these modern warehouse designs also means retraining staff and implementing new operating procedures. In addition, some warehouses (or areas of a warehouse) might be modified to be totally robot-friendly, resulting in exceptionally high-density racking, and other storage features such as low-oxygen environments that aren’t typically accessible to people.
Predictive Maintenance in Industry 4.0
A strategic switch from a reactive to a predictive maintenance approach is one of the many implications of the Industry 4.0 revolution. Process owners may prevent unintended, unforeseen incidents, keep an eye on assets, and manage the entire warehousing system with the help of analytical tools for predictive maintenance.
Managers of warehouses must change their operations procedures to include preventative maintenance protocols. To prevent breakdowns, these systems require precise and timely maintenance interventions. You cannot depend on a run-to-failure operations plan and expect to keep warehouse systems operating efficiently. Companies must employ condition-monitoring techniques when creating maintenance schedules for sophisticated warehouse equipment to ensure prompt discovery of any equipment flaws. Businesses use a variety of data sources to improve internal operations and satisfy intricate market demands as warehouse operations change. This suggests that warehouses must maintain thorough maintenance records and efficiently handle maintenance stocks.
In the coming years, businesses will inevitably look to automate warehouse upkeep. They’ll need to choose and put into practice appropriate Computerized Maintenance Management Systems (CMMS). This consists of centralizing data management utilizing cloud-based platforms and taking advantage of Internet of Things (IoT) sensors to gather real-time data on equipment performance. Companies may find and fix recurrent equipment failures, optimize corrective actions, and strategically manage spare part stocks by automating warehouse maintenance and gathering pertinent performance data, all of which lower operational costs.
Warehouse operations optimization is about the processes that provide you with the results you want in the most efficient way. It gives businesses the capacity to maximize their operations when combined with the capability to simulate the facilities’ behavior. Additionally, it enables the testing of different WMS systems or investment iterations. This is the first—though not the only—collaboration between a “digital twin” of the system and the predictive maintenance platform. Simulating the behavior of the warehouse is possible thanks to the complete representation of the system and its dynamics in real-time. This makes it possible to test the predictive maintenance algorithms in a variety of circumstances, especially those that haven’t happened yet. Such simulations of industrial plant behavior enable quicker and more effective testing of preventative maintenance solutions.
Digital twins, various simulations, and even more detailed data collection can serve both goals of predictive maintenance and operations optimization.
How Can You Take Advantage of This Modern Warehouse Technology?
Take a look into the creation of your own digital twins if you have a strong technological basis in place. Then you can start using features like developing new warehouse spaces based on existing models and testing changes before putting them into practice. It can be a terrific approach to enhance the operational environment of your internal business and the technological infrastructure of your fulfillment partners. Looking for a storage partner who stays ahead of digital disruption at all times? Contact First Line Software.