What Does a Digital Factory Look Like Today? How the Digital Factory Software Impacts Modern Manufacturing?
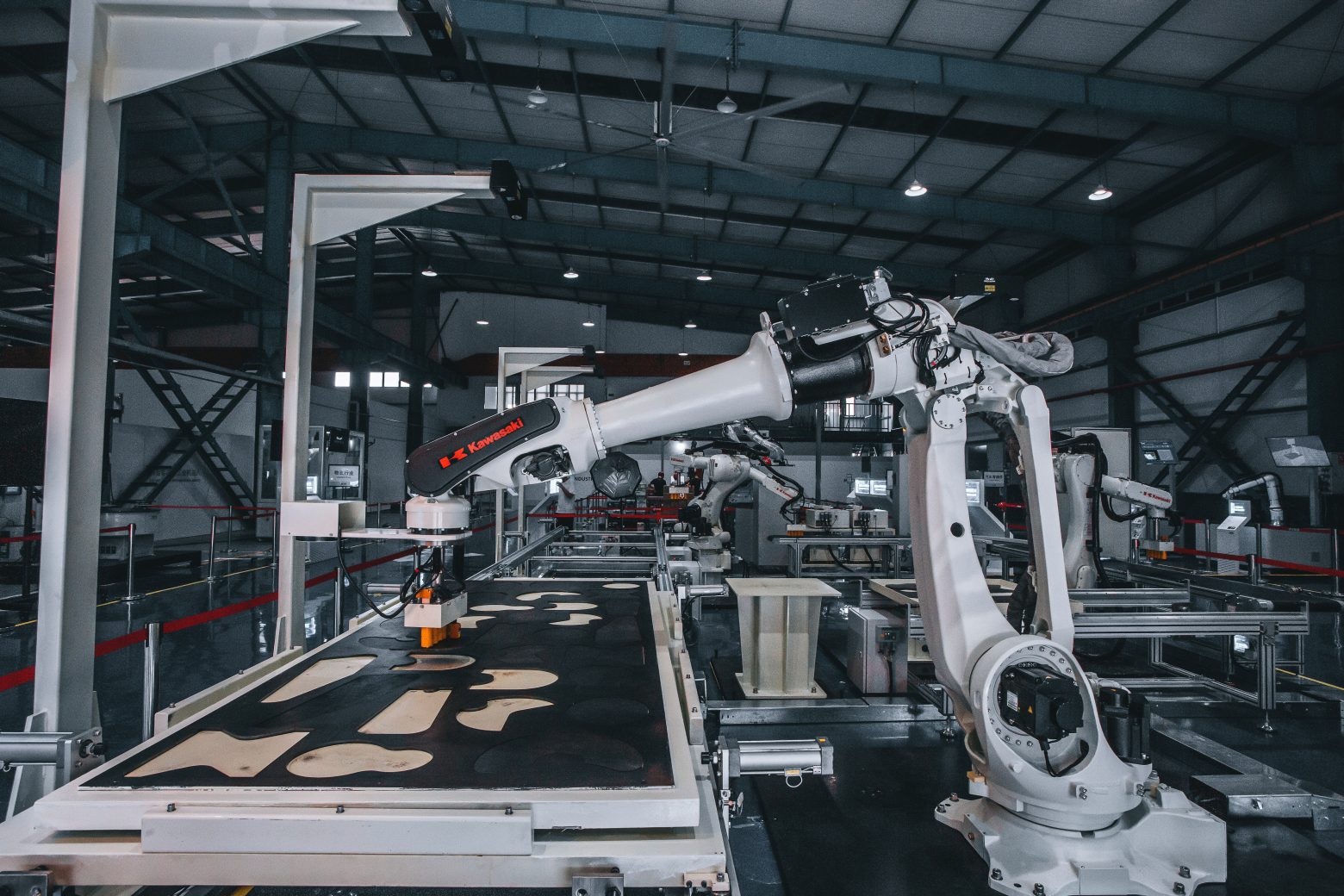
Since the Industrial Revolution, people have been transforming factories and enterprises that drive innovation, and in 2022 we’re only accelerating this evolution. From the spinning jenny to cloud intelligence-powered manufacturing, the factory has always been man’s tool for creating anything and everything our modern society requires to function, now more than ever with the integration of advanced Digital Factory Software.
Industry 4.0 and the Rise of Digital Factory Software
The Fourth Industrial Revolution raised the capacity and efficiency of existing factories and also created new organizational and technical models for them. The digital factory appeared as the central concept of Industry 4.0. In the first stage of digital transformation, individual machines were equipped with sensors and software which turned into cyber-physical systems, now the focus is on their integrated networks. But what exactly does “Digital Factory” mean in today’s lexicon?
Digital factory ideation begins with the way business processes combine to generate high technological results, driven by cutting-edge manufacturing software. This enables a new generation of high-quality, competitive products to be launched within a short period. A new type of manufacturing enterprise runs all the systems and technologies. This includes a new generation of high-resolution sensors, the IoT, machine-to-machine communication, CAD/CAE/CAM, software solutions, robotics, data analytics, ML, and AI.
Today, industrial enterprises are gathering information from their physical and digital systems and optimizing them for the next step in manufacturing. Having adopted big data, AI builds mathematical models for a digitalized end-to-end manufacturing supply chain.
For example, in the past, automobile companies had to destroy about two hundred cars during their crash testing phase before launching a new model on the market. Today’s virtual crash simulation stand can carry out an unlimited number of tests, and explore the potential different crash scenarios (frontal or side-impact, collision with an obstacle, and others). The company does not invest money in the construction of a physical object until it has verified its effectiveness in a virtual environment.
The “Automotive Testing Expo” highlights how software accelerates vehicle development. BMW announced at the expo a new version of an AI software platform called Monolith with self-learning models that fill the gap to instantly understand and predict vehicle performance. It’s an example of how cyber-physical systems begin their life cycle in modern industries and factories. This process, which combines real and virtual objects and is built through digital methods, is called the digitalization of modern factories.
Another illustration of modern digital manufacturing is the global pioneer in the aerospace industry – Airbus. The component production is located in Germany, France, Great Britain, Spain, China, India, Poland, and the USA. The final assembly of the aircraft is based in Toulouse and Hamburg. It’s geographically distributed across many countries, and all design and testing are performed in CAD/CAE/CAM software systems. Airbus built workflows and ecosystems that produced a mosaic of physical elements and digital solutions that culminated at the final point and turned into aircraft.
On every flight, an incredible amount of data is generated constantly by airlines. Millions of passengers, thousands of cities, as aviation companies harvest all the data connected to each airplane. What do you think will happen with all that information? Airbus is creating an open data platform Skywise. It collects a huge amount of data from various suppliers of equipment, parts of the aircraft, companies that provide aircraft maintenance, and the airlines that operate the aircraft. To further their digital manufacturing solutions, Airbus is accumulating absolutely all the information that is connected to the functioning life cycle of their aircraft. This is not the future of digital manufacturing… This is today’s technology already at work.
Data is the Driver of the Digital Factory
The assembly line was the basis of the second industrial revolution, computers launched the 3rd, and data became the basis of the current changes. Digital production, products, and business decisions will primarily take advantage of the collected data.
Today, industrial enterprises are gathering information from their physical and digital systems and optimizing them for the next step in manufacturing, leveraging big data, AI, and machine learning in their digital factory software solutions.
If we talk about infrastructure, manufacturing companies face challenges such as: how to collect information, how long, and where to store it. Now another model of computing has appeared on the technological horizon – Edge Computing. In general terms, this technology shifts remote monitoring and data processing directly onto billions of IoT devices. Smartphones, tablets, sensors, robotics, automated lines, manufacturing, and distributed analytics, produce lots of data. If we utilize a hub-and-spoke example, the cloud is the hub and everything on the outside of the spokes is the edge. When big data processing is at the Edge instead of the Cloud, the cost is reduced.
Typical examples of edge computing include:
- Analysis of video streaming from surveillance cameras
- A fleet manager using edge resources when network access is limited
- Robotics controls
In manufacturing, the technology collects data on equipment, machines, and conveyors and notifies staff when some equipment malfunctions. Edge computing, IoT, and manufacturing software systems inform the main control center whether all operations are running as scheduled. Edge computing serves many devices simultaneously. The collected information can be transferred to the corporate data center as needed for further analysis by managers and executives. The combination of edge computing and industrial IoT devices optimizes manufacturing processes, and supply chains, and creates a smart, digital factory.
To collect information from the real-time manufacturing process, the factory must be equipped with high-quality sensors. The sensors accumulate information through 5G and Wi-Fi and deliver the data to the cloud. The analytics systems are built: BI systems, statistical analysis, OLAP cubes, and visual capabilities for dispatching and monitoring information. A great example of smart manufacturing today is the Big River Steel company, it produces 2 million tons of steel annually, and only 600+ people work there. It is worth noting that the initial investment in the construction of Big River Steel amounted to $1.6 billion.
All this is done with overlapping goals: to produce more products without increasing production costs while delivering increasing profits. The MES (manufacturing execution system) platform provides real-time visibility of production operations. For example, Harley Davidson has reduced their motorcycle production period from 21 days to 6 hours utilizing a modern MES. The company customizes all motorcycles at the client’s request, and the system recalculates the production plan every time there is new input data. Every 89 seconds, a motorcycle rolls off the production line, and every 89 seconds, the production plan for all manufactured motorcycles is recalculated due to a new order.
How to Implement Edge Computing Right Now
Enterprises will invest heavily in edge computing for manufacturing operations, production asset management, and omnichannel operations, among others. In general, global spending on edge computing is expected to be $176 billion in 2022, an increase of 14.8% over 2021.
The transition to edge computing is preceded by a detailed analysis, outlining the need for architecture to seamlessly receive and process data in real-time. Building a channel for transporting sorted information to the central data center is the genesis of a solution.
There are two ways to implement the concept of edge computing in an enterprise: installing physical equipment, including servers and on-premises data collection devices and cloud solutions. Both are offered by industry heavyweights such as Intel, IBM, General Electric, Cisco, and Microsoft. However, there are vendors such as First Line Software that specialize in supplying vertical solutions and IT applications for edge network protection, monitoring, logistics, and factory automation.
Talk to Us Today!
The digitalization of modern factories is no longer a futuristic concept; it’s a reality powered by advanced Digital Factory Software. The integration of data, analytics, and edge computing is reshaping the manufacturing landscape.
Consult with First Line Software to explore how digital factory software can transform your Manufacturing journey, helping drive a step-change in operational performance. It will allow you to make better operational decisions, be more efficient, and realize significant benefits. Our expertise enables asset optimization to reduce energy consumption, emissions, and incident severity while increasing asset life and reducing operational spending.
As your primary IT software partner, First Line Software will drive manufacturing digital transformation.