Will Robots Replace Humans in Manufacturing?
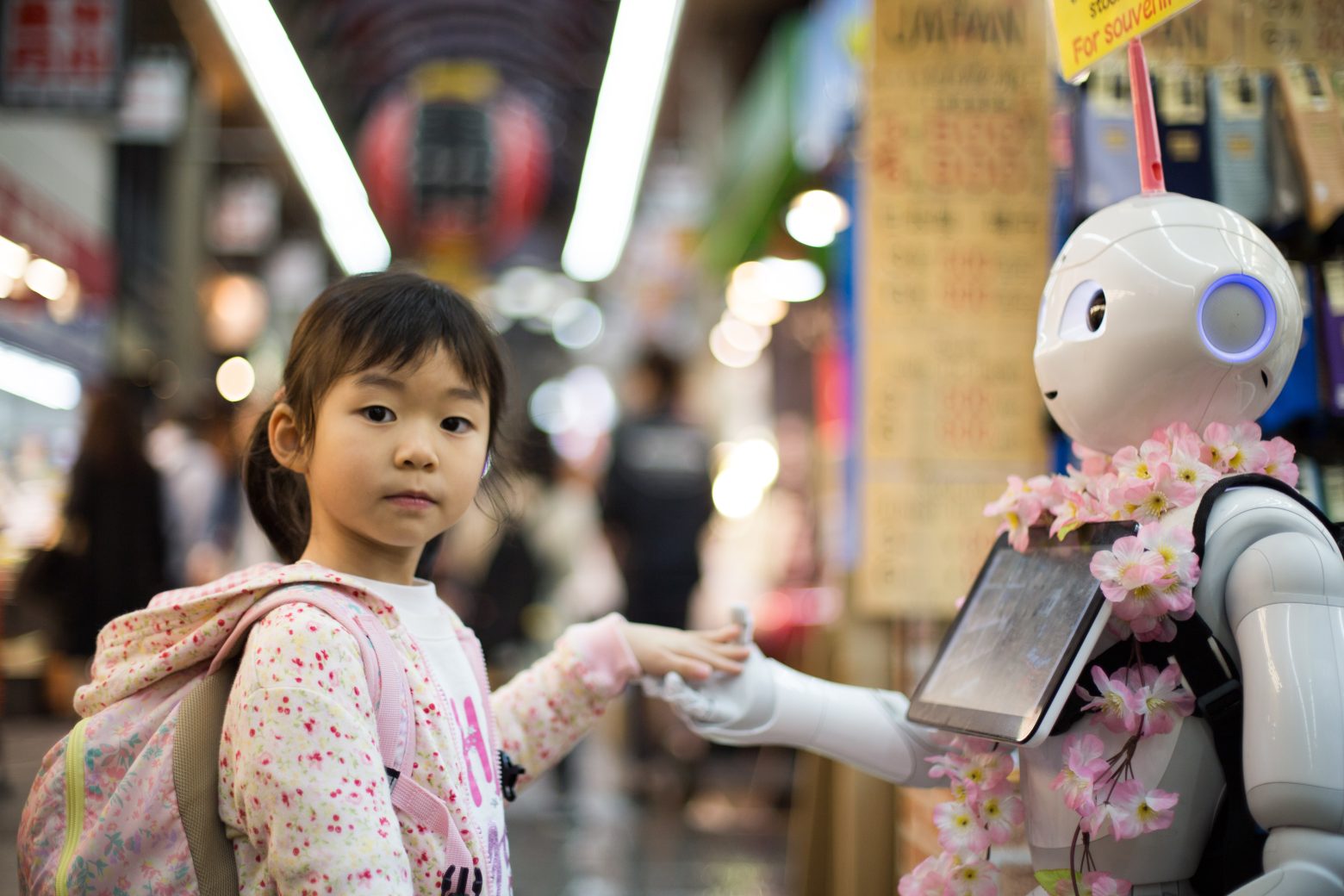
In recent years, robotics and artificial intelligence have been a benefit to nations all over the world. To become one of the top automated nations in the world, there are competitions in artificial intelligence, robotics, and other similar fields. The goal of automation-focused nations is to effectively and efficiently reduce workloads while increasing productivity. However, some people believe that technology and artificial intelligence will replace human workers’ and their jobs, and in some circumstances, this is true. However, machines will never entirely replace the need for people in manufacturing or most other fields of human endeavor.
What the Research is Indicating
Our homes and workplaces are beginning to see the first hesitant steps taken by robots from the manufacturing floor. In a recent analysis, McKinsey’s Technology Trends Outlook 2022 Research predicted that in the next 10 to 15 years, a market for human-sized and-shaped robots might reach $6 billion (or more). By 2030, it is predicted that there will be a 4% labor shortfall in US manufacturing, and by 2035, there will be a 2% increase in the need for aged care worldwide.
The report is important given the explosive growth of the global robotics technology business. Robot purchases in the USA reached a record high in 2021, and by 2028, it is anticipated that global sales would reach $31 billion. The pandemic accelerated the adoption of new technology as businesses sought to minimize costs and adapt new methods of working. Accelerating automation and the effects of the Covid-19 recession have presented a challenge to traditional manufacturing employees.
The Robots Ongoing Development
One of the most automated nations in the world is South Korea. The manufacturing sector in this country is focused on having the highest robot density, which means one robot can handle the task of 15 full-time human employees. To set an example for other nations on automation, it has become among the first countries to enact a robot tax.
The most important thing to understand is which jobs robots can complete more quickly, and which jobs require human interaction – this is what’s at the heart of the disparity. Major automobile factories have nearly fully automated their paint and body operations. These are jobs that frequently pose ergonomic and safety issues for people, and call for regular repetition and consistent quality. Although lead-based paints are no longer used, working in these areas could still expose employees to a variety of hazardous chemicals and dangerous situations, making these the classic kind of occupations robots have been built to tackle.
However, assembly lines continue to significantly rely on a human workforce in order to handle the variety of choices in new models, such built-in vacuum cleaners and interior lighting. With up to 60,000 different parts for the range of electronics and other bells and whistles offered on automobiles, today’s highly customized vehicles demand the adaptability of human workers who can quickly pivot to new needs and developments without extensive computer reprogramming.
Each additional robot placed in lower-skilled regions might result in roughly twice as many job losses as those in higher-skilled regions of the same country, increasing already-growing economic disparity and political polarization. Regions with a higher proportion of low-skilled workers, which tend to have poorer economies and higher unemployment rates, are significantly more vulnerable to job loss due to robots. Furthermore, people who leave manufacturing tend to find new positions in transportation, construction, maintenance, and office and administrative labor, all of which are vulnerable to future automation.
However according to 57% of manufacturers, robots are supplementing human labor rather than replacing it, adding power and precision. The majority of companies that use robotic technology find that it improves the jobs performed by their human employees.
This data point demonstrates how, as manufacturers struggle with inflation, persistent supply chain challenges, and extraordinary labor shortages, humans are increasingly working alongside robot coworkers after the pandemic. Most manufacturers only want to automate additional processes, which may include using robots to complete routine, repetitive, or especially dangerous activities.
Humans and Robots in Tandem
Various industries like manufacturing, retail, transportation, and communication have benefited from automation. Robots may now be found everywhere, from car factories to hospitals, helping to carry out tasks like brain surgery or inserting computer chips into gadgets. Automation now includes robots and artificial intelligence in addition to just mechanical and electrical systems.
Economic data showing that manufacturing automation has increased since the pandemic’s start is unquestionably an indication that the sector is embracing innovation. The settings in which they operate, however, must also change as the machine workforce does.
Manufacturers must provide an environment that supports this new hybrid workplace in order to maximize their investments. To do this, producers must design workspaces where humans and robots may collaborate in close proximity to maximize available space and boost output.
In many ways, human roles are being enhanced by robots rather than being eliminated. Automation frees up humans to accomplish more complex jobs, like interacting with clients, inventing better products, and even servicing robots themselves by automating.
Given all of this, it’s not surprising that there has been more than a small rise in human-robot interaction during the past year or more. It only seems logical that human and automated coworkers are interacting in the workplace as manufacturers speed up their use of automation and keep introducing warehouses with robots.
Customization is King
Let’s take a look at one of the newest and most personalized vehicles being produced by a U.S. automaker in a North American manufacturing facility. At this facility, automation and robotics have long been welcomed and the corporation has expanded the number of robots there to more than 1,000. However, over the past ten years, the number of plant employees has only decreased by approximately 8%.
Why were so many people still employed over those 10 years? The latest model’s extensive customization and the manufacturer’s astute realization that having robots and automation re-programmed all the time to suit constantly changing needs may have delayed production, and at the very least, increased the cost of the shift. These were the decisive factors in keeping more people on the factory floor.
Even though automation will ultimately have a revolutionary influence, according to the lessons learned by the car industry, change must be gradual. Managers should not automate huge swathes of operations at once just for the sake of efficiency when introducing bots and automating processes. Instead, they should try to solve individual problems by deploying other low-cost solutions that may simply be people.
A New Robot from Amazon
An important step in the e-commerce giant’s efforts to lessen its reliance on human order pickers who currently play a key role in getting products from warehouse shelves to customers’ doorsteps, is the development by Amazon. of a robot capable of identifying and handling individual items.
Sparrow is the name of the robotic arm, which is topped with retractable suction cup-like attachments. The device can move objects of various shapes and sizes out of a plastic tote and into other containers on its own. The bot can manage millions of different products. Even while such jobs appear straightforward, automating them has long confounded Amazon roboticists. Hundreds of thousands of people are employed by Amazon, and they now choose and pack products more swiftly and accurately than machines thanks to their manual dexterity and intuition. Robots like Sparrow, if extensively implemented, might eventually render substantial segments of that workforce obsolete, shifting the emphasis away from employees who execute repetitive and monotonous jobs that require little training, toward a presumably smaller number of technicians who monitor and maintain these robotic systems.
Amazon has long aimed to have the majority of its warehouses automated. However, the business has been cognizant of the notion that it intends to remove jobs. Amazon’s leadership put a lot of emphasis on the new roles that increasingly automated facilities would need, and they predicted that many front-line workers would undergo retraining for these more highly specialized positions.
In 2022 there are approximately 350,000 robots at Amazon across all of their facilities.
Who’s Crucial in the Future?
With the transformation of physical infrastructure, the repatriation of offshore skills, the increase in self-service and virtual services, and the closer integration of clients and robots, this robotic revolution is expected to bring about significant changes. As people shift into a new breed of professionals with both business and technical abilities, who can manage both bots and humans in the future, businesses will need to provide employees with new roles and responsibilities, training, and even new career pathways. Managers should always keep in mind that the most adaptable kind of automation is people. They are completely capable. All you have to do is train them. Contact us to be agile in your own Manufacturing AI transformation!