How to automate your warehouse
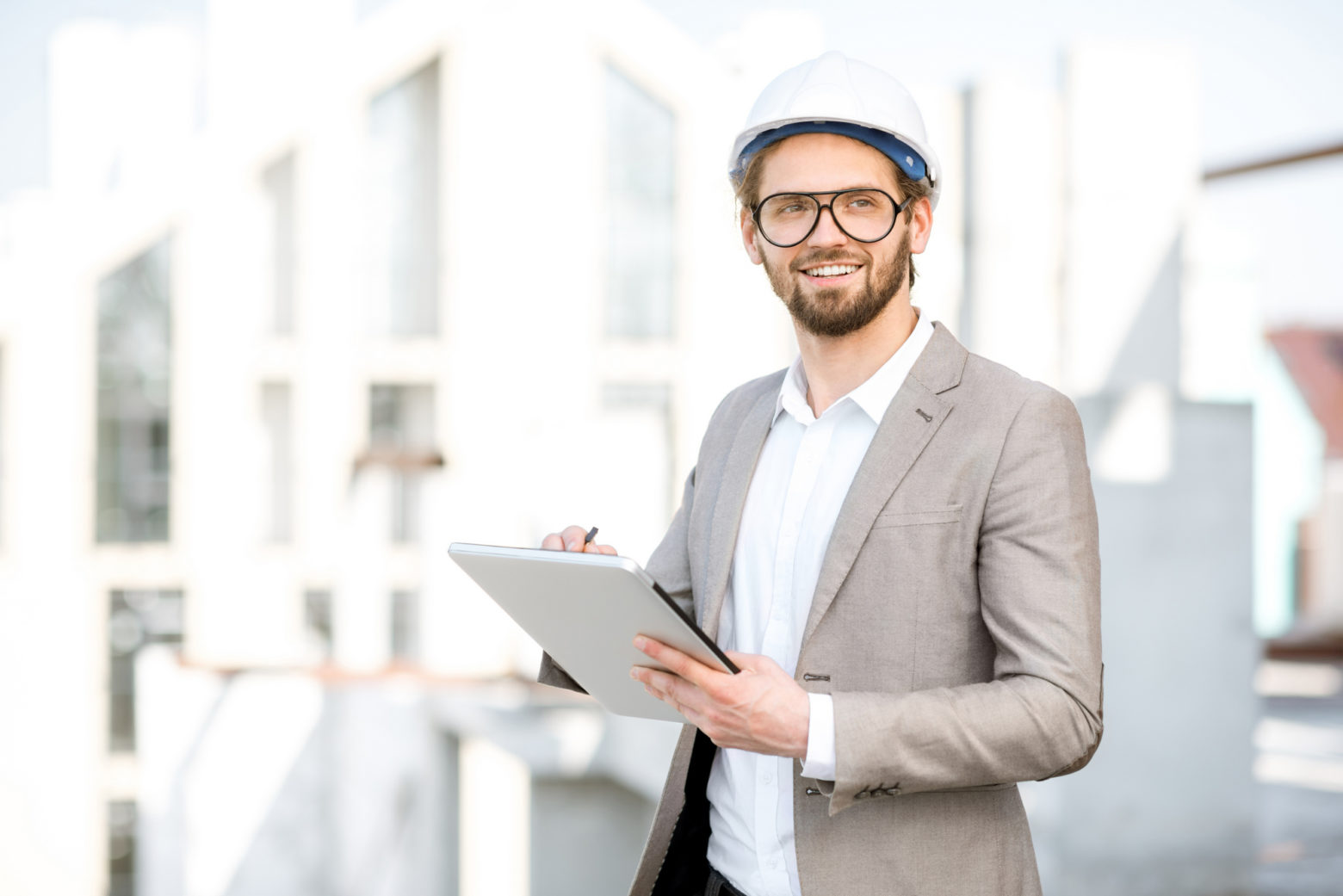
In response to the question “Do I automate my existing warehouse process or do I change my process altogether?”, our expert of the WMS team offers Logistics Business readers his exclusive thoughts.
There are countless quotes from across the globe and time about ‘change’. I’ll spare you my favorites as we’ve all heard them before, but fundamentally we all accept the one constant in our lives is change. Without becoming too philosophical in an article about Warehouse Management Solutions, understanding change and how it applies to the decision-making process of automating your warehouse is what I’ll be sharing with you in this article.
People are conservative by nature and changing the way we’ve been doing things never comes easily. This might especially be true in your company where the decision to automate your warehouse has been made. You’ve recognized the efficiencies that automation brings to your organization, and demonstrated due diligence to the powers-that-be that the investment is sound. However, as much as those reasons for automation make sense, it’s still likely to come with its own set of challenges such as, HR issues, the financial expense, and the actual change to processes that automation brings with it.
Embrace change
Even though it’s in our nature is to minimize change, let me explain how embracing change when it comes to automating your warehouse can pay off in ways you may not have considered before.
It starts with the ever-difficult task of looking within your company to define your business processes. This comprehensive front-end business introspection combined with a careful WMS (Warehouse Management Solution) partner selection will help determine the optimal configuration of your space, and the necessary equipment to make it work.
Statistically speaking, your warehouse is likely to be mostly manually operated; research shows that 80% of current warehouses are still manually operated with little to no supporting automation. Just 5% of existing warehouses are fully automated-meaning completely robotized. Therefore, people are the primary movers of goods and materials throughout the facility, perhaps with some equipment and systems to help the process along.
This “process” is where you need to begin your analysis. For some clients, the underlying premise might be that in their manual warehouse, the daily execution and regulation of the process is their strength. Other clients may come to the conclusion that their existing process is a weak point and needs redoing.
People, unlike automated technology, can work relatively efficiently under somewhat structured guidelines. In a manual warehouse, processes are more often than not invented on the fly with circumstances dictating the immediate need for action. This is essentially a creative attempt to control chaos in the warehouse by finding optimal solutions to various problems at specific points in time.
How to automate?
Once this basic premise is accepted, the in-depth analysis of your current situation should begin by asking two very important questions:
1. Do you fully automate your warehouse based on the existing processes? Or
2. Do you implement current automation industry standardized processes?
Let’s cut to the chase here and state that the preferred approach in most cases will be to implement current automation industry standardized processes whenever possible. In many European countries and elsewhere in the world, there are certain benchmarks or standardized criteria to be met when implementing a WMS. However, this may not always be feasible or practical for a variety of reasons as we’ll see shortly. In the meantime, let’s review some of the Pros and Cons for each of the two approaches:
Do you fully automate your warehouse based on the existing processes?
Pros:
- The specific problem that exists gets solved;
- No significant additional changes need to be made to the workflow;
- Integrating with existing systems is easier by being more compatible with the existing processes implemented in those systems;
- There is no paradigm shift – Remaining employees learn more easily with less resistance, and training is less expensive.
Cons:
- With this approach, we keep both explicit and latent problems in the existing business processes. Moreover, they become less obvious, while retaining their negative impact on the overall performance of the system;
- Lock-in in such a system is much higher. Problems arise not only when switching to a fundamentally new WMS, but even upgrading to a new version of the same system can be expensive and difficult since it’s usually now a proprietary WMS solution;
- The qualifications of easily accessible people who can support the system must be high;
- Over time, institutional knowledge of this proprietary system will become lost either through staff attrition or lack of documentation making repairs or upgrades difficult;
- This kind of customisation (actually creating a new system) is expensive, since you’re basically paying to develop a new, bespoke system which is ultimately more expensive than starting with a standardised solution.
Do you implement current automation industry standardized processes?
Pros:
- This approach will almost always be faster and cheaper to implement since there is less custom development involved;
- Any updates will also be faster and cheaper to put into place;
- It will be easier and less expensive to integrate with new external systems and equipment since standard solutions are more likely to have built-in functionality to integrate with standard processes of other systems (ERP, MES, etc.);
- If there is a need to replace one WMS for another, standardization makes it much easier;
- Modifying the current process in order to comply with industry standards may resolve latent problems, in-turn embracing world-accepted best practices.
Cons:
- There will be significant breaks in established processes that will deviate from the ‘usual way of doing things’;
- A potentially more expensive training process and possible personnel resistance;
- There are conceivable risks of complex integration with existing specific legacy or self-written systems. When replacing one proprietary system, there is a chance that other non-standard systems integrated with it will also need to be replaced or modified.
Everything is a Compromise
As I mentioned earlier, the preferred approach should be to implement current automation industry standardized processes whenever possible. However, this may not always be feasible and in reality, it’s often necessary to find optimal compromise solutions when existing warehouse automation is partial, or a simplified accounting process for goods is being implemented.
Compromises such as these are due to the fact that sometimes when you’re simulating a full automation scenario in your warehouse (which you should always do) it may reveal the emergence of complex, ineffective processes, without which the final system significantly benefits.
If you try to fully automate everything, it might be less efficient than not automating a process. The simulations your WMS vendor creates and runs may prove not to be the most efficient based on what’s really happening in your facility. Real processes in real warehouses still differ from the mathematical models of these simulations. This is why compromises will always exist.
Let’s examine one example of this compromise keeping in mind that there can be many processes that under certain circumstances may not allow for 100% automation.
A real-world situation of a WMS compromise can be seen in the warehousing putaway process.
Putaway refers to the physical act of moving incoming inventory from the receiving zone to an optimal location for storage. This process often requires customization, which may not always improve efficiency if not properly approached since it can’t usually be fully automated or standardized.
As Delivery Director for First Line Software; here’s an actual account of that particular scenario that I’ve run across.
A client had a fully automated warehouse process that had a complicated accounting system for tracking goods, which included integration with several manual processes; this further caused numerous errors and slowed down the entire process by 3-4 times. As a solution, we recommended abandoning the tracking of goods at intermediate points. The goods were initially registered upon receipt, and then finally when they appeared on the warehouse shelf. This task was placed under the responsibility of the team managing the putaway process as opposed to trying to integrate it into the automation flow.
Where Do You Begin Automating Your Warehouse?
Now that I’ve shown you the pros and cons of both approaches to WMS implementations and the inevitable compromises they might bring, let’s review a few key strategies to guide you in planning a comprehensive warehouse automation makeover.
- Don’t make a hasty decision to preserve your existing business processes without first analysing and comparing them with other world-accepted best practices.
- Choose a system that has a standardised functionality that completely covers the business processes of your warehouse and is recognised in the industry.
- If a decision is made to customize within your existing WMS, you need to assess how much this customisation changes the architecture of the system. If the underlying architecture does not change, then it is easy to connect or disconnect the custom features. Excessive customisation can complicate maintenance and further upgrades.
If you think about it, the decision to automate your warehouse becomes an opportunity to increase the efficiency of your organization as a whole by standardizing processes. The introspection about change regarding how you have done things vs. how you want to do things becomes very important. You’ll likely find untapped efficiencies when each business process is considered sequentially and systematically. When these steps are all carefully documented, you’ll find it much easier to evaluate whether to keep the existing processes or change and adopt a new, standardized methodology when automating your warehouse.
Source: Logistics Business
Learn more about our Warehouse Automation Expertise and Warehouse Intralogistics Events