Liebherr Tower Cranes Warehouse Plant Automation
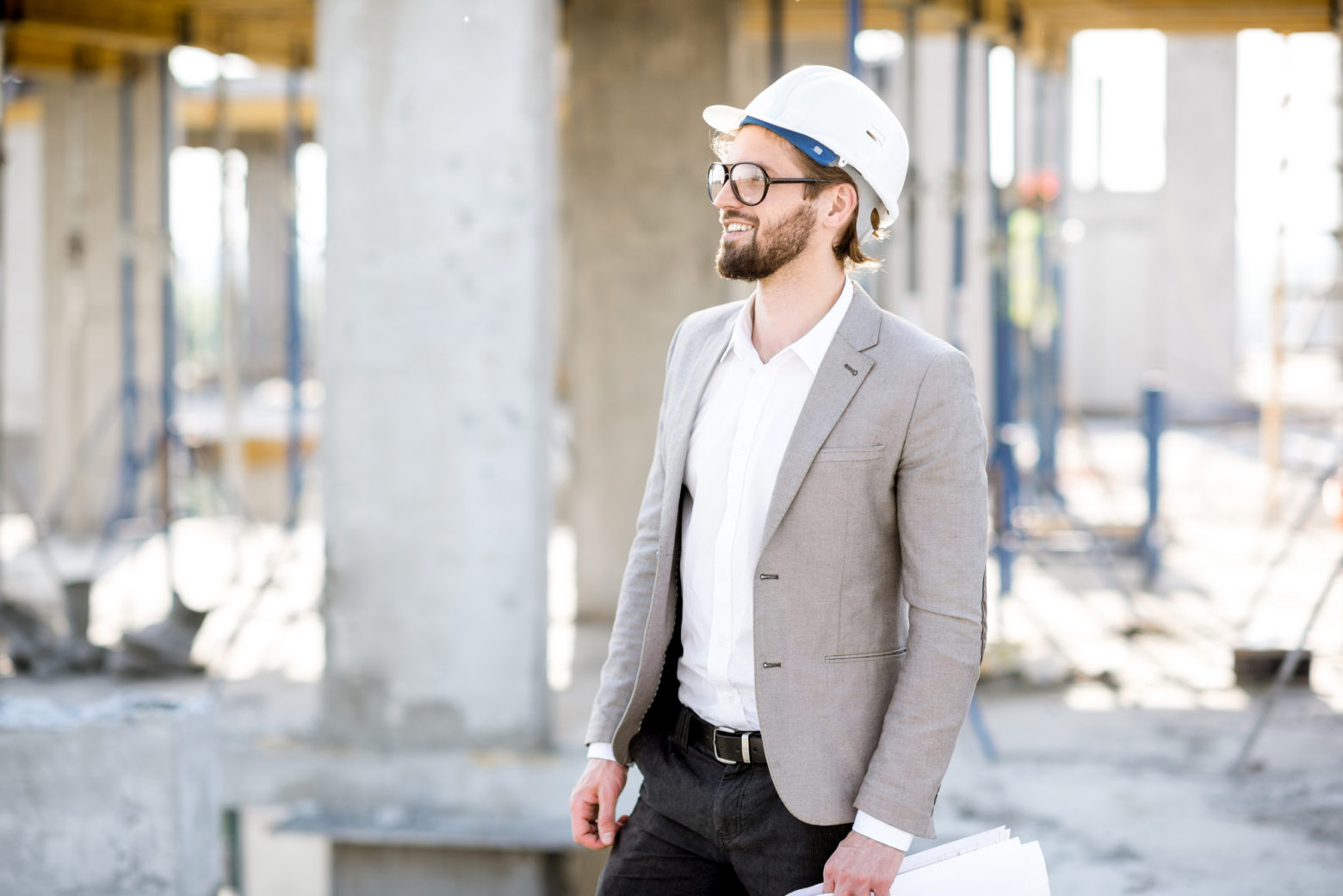
The Task
The Liebherr-Werk facility includes processing and assembly departments of industrial tower cranes and the temporary storage of crane parts. Liebherr-Werk operates in a piece-production format which means that the cranes are manufactured according to customer specifications. The crane parts, including huge units weighing up to several tons, are produced individually in different sections of the plant. Each component is assigned an item number for location tracking purposes and to indicate the specific tower crane that uses the part.
Prior to the implementation of the system, there was no automation at the warehouse. Paper records were used to control the parts and unit storage on specific racks.
Early in 2014, the Liebherr-Werk management team made a decision to automate the warehouse. The German company viastore WMS Systems GbmH, a global leader in “turn-key” intralogistics systems, was selected as the vendor to implement the viastore WMS, handheld terminals, and desktop stations. Equipment customization was performed by the First Line Software specialists – an official partner of viastore WMS systems.
Project Development
The project was completed over a period of 6 months. The work team consisted of three specialists: a project manager from viastore WMS and two First Line Software engineers. Individual storage racks were linked in a unified information system, the loading and distribution processes were automated, and integration with the ERP (Enterprise Resource Planning) system was completed.
One of the project challenges was the absence of a standardized rack format. Temporary warehouse positions at Liebherr-Werk were created in the 1970s when no automation was planned. As a result, there is a vast diversity in shape and size between the racks. The new system includes functionality for supporting each type of rack.
The Results
A project involving custom assembly provides equally specialized results.
- Automation of the warehousing area eliminated the need for paper records and streamlined the process for parts distribution and temporary warehousing.
- The system organizes the parts to ensure that their distribution to the assembly department is performed from the same location within the warehouse.
- Over three thousand storage positions are managed by automation.
- Assignment of item numbers and parts transportation logistics were also automated.
- A virtual record of all large parts now exists.