viastore WMS System Implementation in a Class “A” Pharmaceutical Center Warehouse
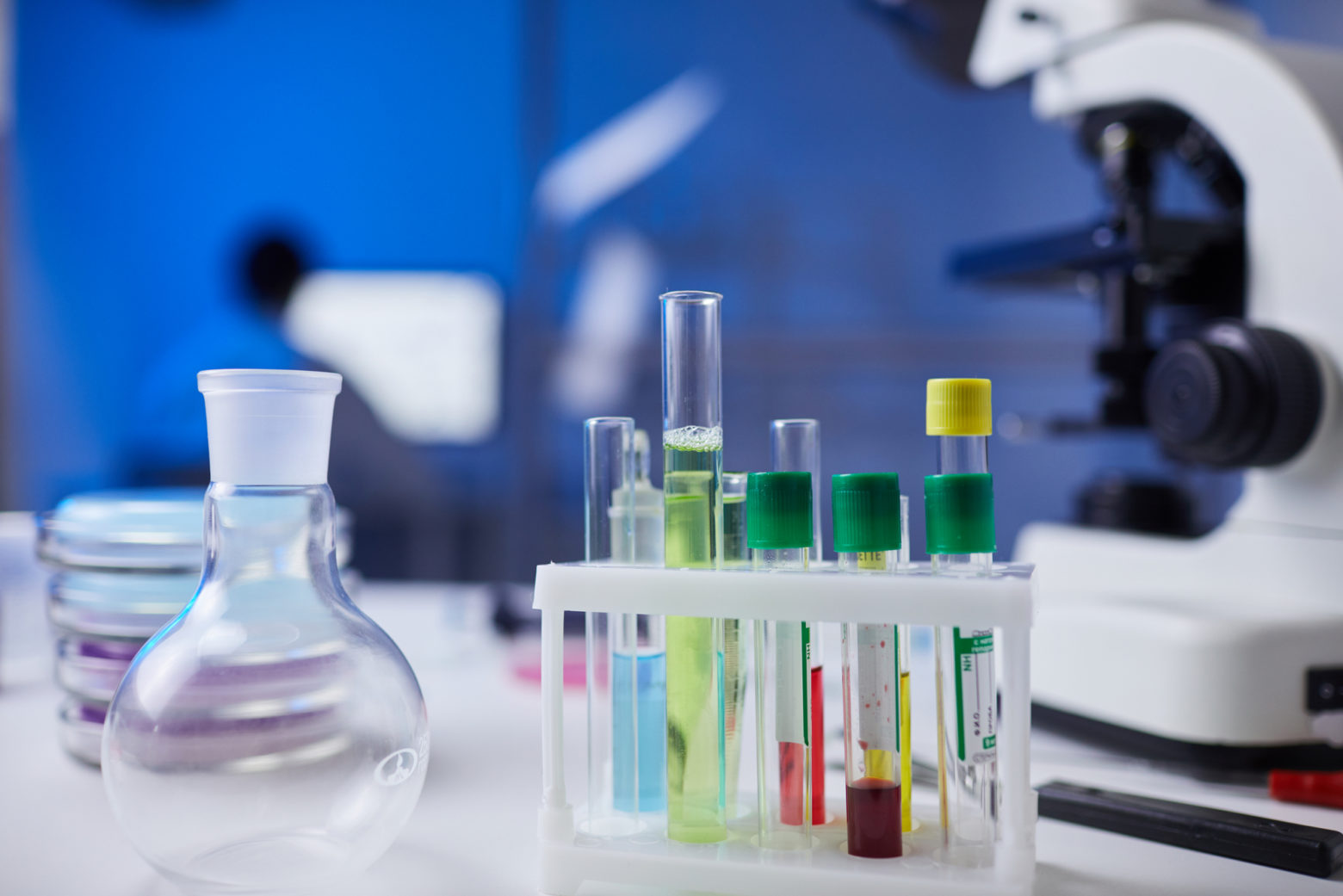
The Client
The company specializes in the distribution of pharmaceutical products and consumer goods for the health and beauty industry.
The Problem
Our client started construction of a new pharmaceutical warehouse (30,000sq. meters). The warehouse is categorized as a class “A”, with advanced, automated methods of picking orders and a general level of automation of around 40% for its assembly process. In less than two years the warehouse was opened.
The Client сhose a management system on the Germany-based viastore WMS systems GmbH recommendations. In addition, the selection and packaging of small pharmaceutical production technologies included the equipment, A-Frame, and Pick-by-light by the Austrian company Schaefer. Overall systems implementation was provided by a group of specialists including viastore WMS and First Line Software as the exclusive partner of viastore WMS.
Project Development
For a pharmaceutical warehouse, the small-piece order collection was complicated by requirements of both lot-based and serial accounting. This means the interaction between automation and the personnel’s work is balanced more reasonably, thus the probability of mistakes and re-grading is less.
For the selection process and packaging of small pharmaceutical products in the warehouse, the client decided on the following key advanced technologies:
- A-Frame – the automated system that matches orders of high productivity with minimization of manual work.
- Pick-by-light – devices which help pickers select the order in the semi-automated simplified mode, being completely paperless.
- Pick-to-belt – the technology of selection of boxes on the conveyor that allows considerable minimization of the movements of the sorter.
One thing that is unique to a pharmaceutical warehouse is its difficult topology. For the storage of narcotics and toxins, enclosed areas are utilized and for perishable goods, special temperature zones and conditions are needed.
Within the project, the First Line Software team integrated the solution of viastore WMS with the Schaefer equipment. The team also established cooperation between WMS and the above-mentioned technologies and integrated the WMS system with the customer’s accounting system. Techniques for the replenishment of zones and statistics of performance and loading of workstations in a selection zone all underwent automation. Handling of serial accounting, working in narrow-passage zones, and ensuring the handling of products with special requirements for temperature storage were all accomplished. The entire movement of medicine on a continuous cold chain was successfully automated.
The Results
- The project started in January 2014 and concluded with putting the warehouse into operation in March 2015.
- From the first workday at the new warehouse, all operations are performed under the control of viastore WMS software in cooperation with First Line Software.
The Technological Stack
- C++, Qt
- Relational databases
- Distributed client-server architecture
- Networking technologies (TCP/IP, FTP, web technologies)