Advanced Warehouse Management: Best Practices for Temperature Control & Intralogistics of Perishables. Part 1

Director of Operations
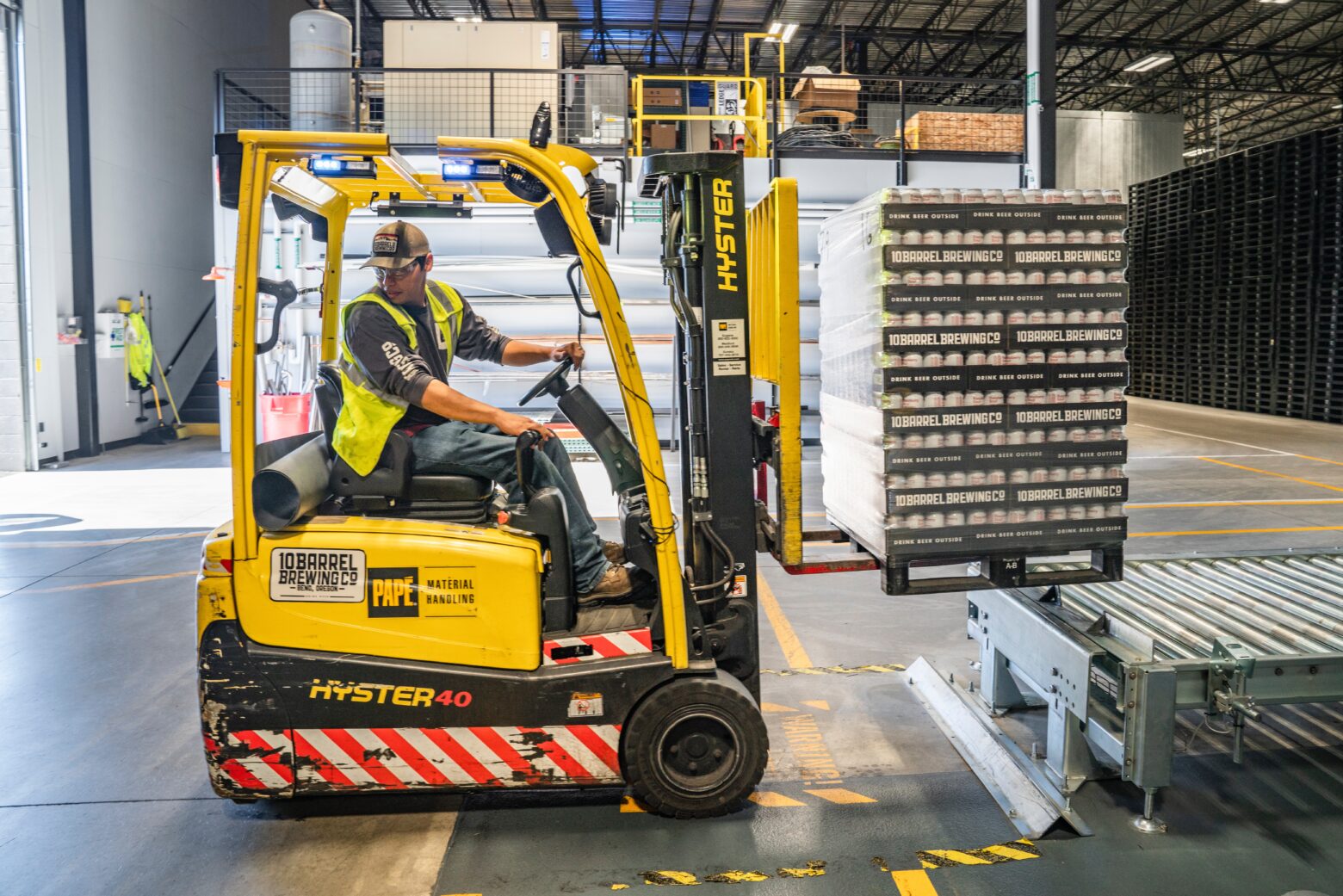
A refrigerated warehouse is a specialized facility designed to preserve perishable items such as food, fresh flowers, select cosmetics, and pharmaceuticals. These facilities are particularly important in urban areas where there’s a high demand and turnover for temperature-sensitive goods. In the U.S. alone, sales in the frozen food market have exceeded $72 billion.
As demand has grown, so has the interest of investors looking to establish new facilities. However, the creation of these warehouses must strictly adhere to industry standards, necessitating the implementation of Warehouse Management Systems (WMS) and IT systems for process optimization.
Given the significance of refrigerated warehouses, it’s vital to understand their components and operation.
Key Components of Effective Cold and Frozen Storage Warehousing
Maintaining the integrity of temperature-sensitive goods, from food to pharmaceuticals, demands a keen understanding of the critical components and practices in refrigerated warehousing.
- Distinct Storage Zones: Effective warehouse organization necessitates clear segmentation. This includes:
- Quarantine areas for items that may be potentially hazardous or need verification.
- Designated sections for expired products, ensuring they don’t mix with valid inventory.
- Varied temperature zones, tailored for different types of goods. For instance, dairy products and certain pharmaceuticals might have different temperature requirements.
- Integrated Technology Platforms: Employing Warehouse Management Systems (WMS) and advanced IT solutions not only optimizes processes but also offers real-time insights into inventory levels, product movement, and storage conditions.
- Uninterrupted Cold Chain Management: It is imperative to maintain a continuous cold chain, ensuring goods are never exposed to temperature fluctuations that might compromise their quality.
- Constant Monitoring: Real-time monitoring of storage conditions becomes critical in these settings. Automated systems can trigger alarms during temperature deviations, ensuring swift corrective action.
- Efficient Turnover Protocols: Given the nature of perishable goods, a high turnover rate is expected. Efficient systems need to be in place to handle above-average turnover, minimize wastage, and optimize storage space.
Optimizing Temperature Control and Movement
Central to a refrigerated warehouse’s success is the rigorous maintenance of temperature specifications. While specific control systems manage parameters like temperature settings, air humidity, and lighting conditions, the Warehouse Management System (WMS) plays a crucial role in optimizing product movement in response to these factors. Should anomalies arise, the system can prioritize and streamline tasks, directing employees toward swift and efficient corrective measures.
Time is another crucial factor. Minimizing the duration perishable goods spend in loading areas, as well as their transit time within the warehouse, becomes essential. With a WMS in place, the selection process is designed to limit exposure to external conditions, safeguarding the goods’ internal storage temperature.
Consider a situation where products, during shipping, are exposed to warmer external air. Addressing this can be done manually or through automated tools. Yet, manual intervention has its downsides. In an environment where the storage temperature is extremely cold, the movement of an employee equipped with the necessary protective gear becomes restricted, complicating tasks like button operation. Automated solutions like voice-controlled forklifts can streamline processes, ensuring quick product delivery.
Moreover, sometimes just utilizing the warehouse isn’t enough. Services like cross-docking can expedite perishable product delivery without the need for extended storage. This holistic approach to services empowers businesses to address primary concerns without being mired in logistics.
Therefore, the WMS system must streamline product movement, ensuring goods are minimally exposed to non-optimal temperatures, even if this means re-strategizing traditional movement patterns.
Monitoring Product Temperature Compliance and Inventory Management
Monitoring the conditions and whereabouts of goods within a warehouse is essential. Reports that track the position and temperature history of specific items within a designated range ensure these goods haven’t stayed outside their appropriate storage zones for extended periods, thus safeguarding their quality and integrity.
An effective Warehouse Management System (WMS) should also be capable of tracking product expiration dates and taking these into account when selecting items for shipping. When it comes to cold storage, one of the challenges is managing the flow of goods in a manner that prioritizes items with closer expiration dates for sale. Such an approach ensures products with shorter shelf lives are dispatched before they expire, reducing wastage and ensuring product quality for consumers.
In cases where some products experience low demand and linger past their expiration dates within the warehouse, it becomes necessary for the WMS to handle procedures such as automated recycling or disposal.
Ultimately, these measures are a part of ensuring the consistent control of the cold chain throughout the goods’ journey within the warehouse.
In essence, these measures collectively contribute to the consistent control of the cold chain, ensuring the quality and integrity of goods throughout their journey within the refrigerated warehouse.
In Part 2 of this piece, we’ll see how evolving technological trends are pushing the boundaries of advanced warehouse management to preserve the integrity and quality of perishable goods.
Learn more about our Warehouse Automation services.