Key Considerations for Sheet Metal Warehousing

Director of Operations
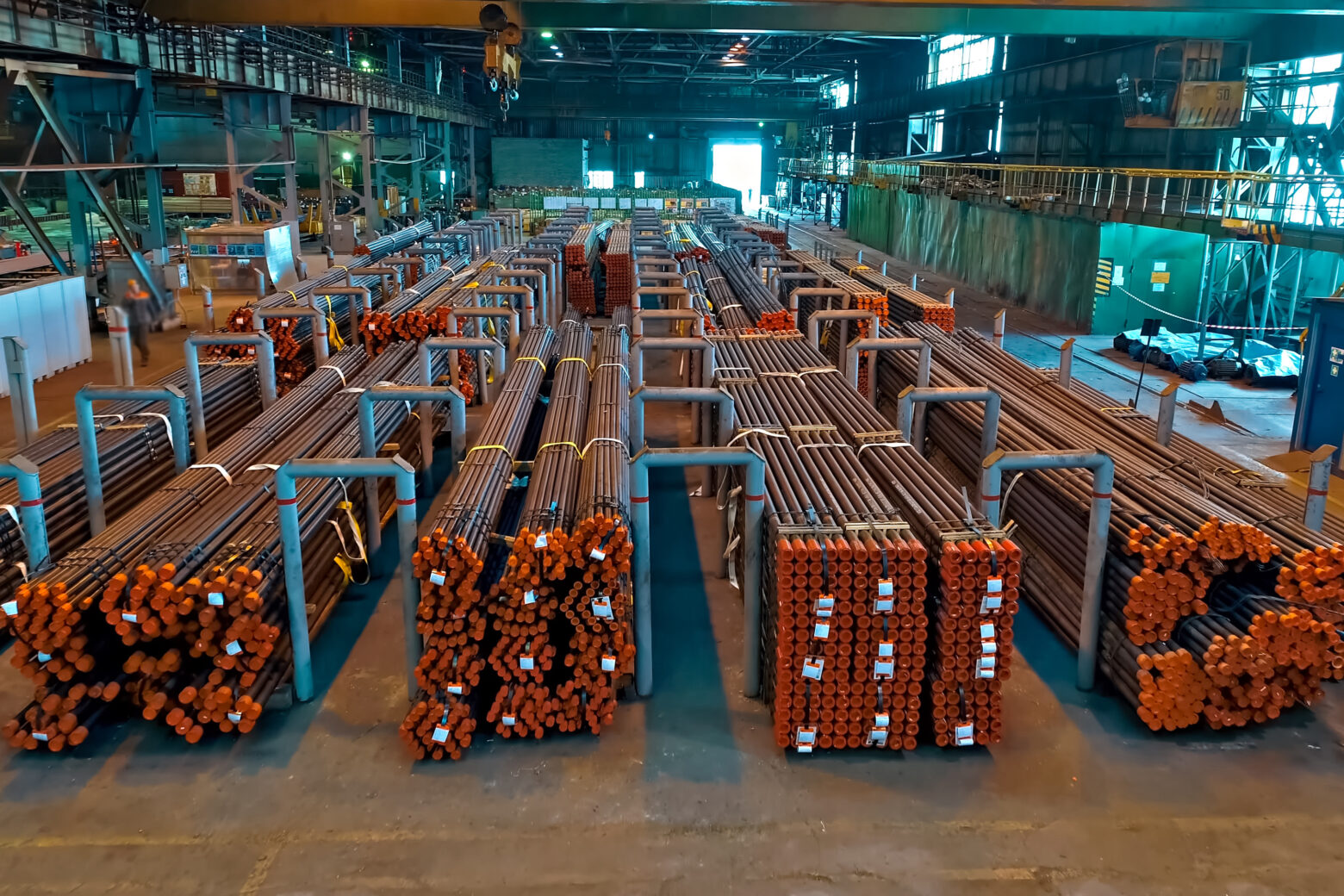
Sheet metal presents a complex warehousing challenge. Its oversized dimensions, inherent safety hazards due to potential weight, and susceptibility to damage from falls necessitate careful planning and implementation. To navigate this unique storage landscape, let’s explore key features to consider and how a warehouse management system (WMS) can optimize operations.
Safety First
Implementing proper safety measures is paramount: including clear signage, designated walkways, adequate lighting, and employee training on safe handling practices.
The safety of personnel and the integrity of the sheet metal itself are major concerns in warehousing operations. To prioritize worker safety, clear walkways, designated areas for maneuvering large sheets, and proper training on handling techniques are essential. Additionally, protective equipment like gloves, safety glasses, and sturdy footwear should be readily available and worn at all times.
Robots can handle the safety tasks to keep human employees away from dangerous places. The robot’s navigation system is a critical factor for success. To flawlessly operate within a dynamic warehouse environment, the robot needs to navigate efficiently and safely. This necessitates employing a robust combination of sensors, cameras, and mapping technologies. When selecting a robot, carefully consider the types of obstacles present in your warehouse. Choose a navigation system equipped to handle those specific challenges, ensuring smooth integration and optimal performance within your unique environment.
Furthermore, preventing product damage requires a multi-pronged approach. Utilizing appropriate storage solutions like mechanical lifting devices, designated racks, and secure straps minimizes the risk of scratches, dents, and deformations. Implementing careful handling procedures throughout the receiving, storage, picking, and shipping processes further safeguard the product from harm. This focus on safety and product protection not only ensures the well-being of employees but also minimizes potential losses while maintaining the quality of the sheet metal for its intended use. The priority is to deliver sheet metal in pristine condition.
Balancing Capacity and Footprint
Sufficient capacity ensures safe and organized storage, eliminating the need for unsafe practices like stacking sheets precariously near aisles. This promotes safe goods movement and minimizes the risk of accidents.
However, maximizing capacity shouldn’t come at the expense of warehouse space utilization. By leveraging vertical space through solutions like high-bay racking or cantilever systems, you can significantly minimize the overall storage footprint. This not only optimizes space usage but also improves accessibility and picking efficiency. Striking the right balance between these two factors allows you to achieve a safe, organized, and space-saving sheet metal storage solution.
Storage Organization and Handling for Sheet Metal
Due to its unique properties, organizing and handling sheet metal within a warehouse requires careful consideration. Unlike many other materials, sheets lack grips or handles, making them slick and challenging to maneuver without proper equipment. To ensure safe and efficient storage, appropriate methods for both organization and handling are essential.
Inventory organization typically involves racking systems or stacked storage, with the option of horizontal or vertical orientation. Each method offers advantages and needs to be assessed based on factors like sheet size, weight, and access frequency. Regardless of the chosen method, it’s crucial to utilize a labeling system to facilitate efficient identification and retrieval of specific sheets.
Material handling systems play a vital role in safe and efficient sheet metal management. Due to the lack of handles, specialized equipment like overhead cranes, magnetic lifts, or vacuum lifters are often employed. Selecting the appropriate equipment is crucial, taking into account sheet size, weight, and specific handling needs within the warehouse environment. By implementing these essential measures, you can ensure organized storage and safe handling of sheet metal, minimizing the risk of damage or injuries.
Seamless Integration with Material Handling
Choosing a sheet metal storage system that works in harmony with your existing material handling equipment is crucial for efficiency and safety. Regardless of your preferred method, be it vacuum lifters, magnetic devices, sheet hoists, or forklifts, the racking system must present sheets at a readily accessible angle for connector attachment.
This doesn’t necessarily require a traditional horizontal storage system where sheets lie flat with one facing the ceiling. Roll-out vertical racking is a prime example, as it exposes the entire sheet surface for easy access to the most common handling equipment.
Flexibility for Manual Access
While automated systems offer significant advantages, maintaining some flexibility for manual access can be valuable in any sheet metal warehousing operation. Some sheets might be small and lightweight enough for safe manual handling, potentially proving faster than waiting for a lift or accommodating equipment maintenance.
Therefore, consider sheet storage systems that cater to both manual and mechanical lifting. Ideally, the system should minimize pulling or sliding movements during sheet retrieval, which is another benefit offered by roll-out racks. By incorporating both automated and manual access options, you ensure adaptability and a smooth workflow in your warehouse environment.
What’s Next?
Next time we will discuss mastering automotive spare parts warehousing. Ready to streamline your sheet metal storage and optimize your warehouse operations? Our experts can help you:
- Audit your current warehouse processes and identify areas for improvement.
- Recommend the best WMS solution tailored to your specific sheet metal storage needs.
- Ensure seamless integration with your existing manufacturing facility.
- Develop a customized implementation plan to minimize disruption and maximize efficiency.
Do you have any questions? Contact the First Line Software team to get a free WMS consultation!